1、Overview
Slewing bearing is a kind of large-scale bearing which can bear comprehensive load, and can bear big axial, radial load and overturning moment at the same time. The slewing bearing is widely used in the real industry. It is called“The joint of the machine”, also need to bear the axial force, radial force, tipping moment of the mechanical necessary important transmission components. With the rapid development of machinery industry, slewing bearing has been widely used in marine equipment, engineering machinery, light industry machinery, metallurgical machinery, medical machinery, industrial machinery and other industries.
Structural classification of slewing bearings
1) Single Row Four Point Contact Ball Slewing Bearing
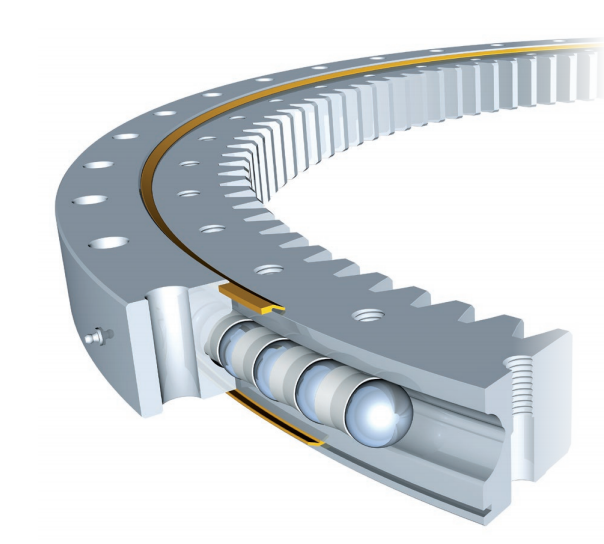
Characteristic of structure, performance and application
The single row four point contact ball slewing bearing is composed of two seat rings, which design in compact structure and light weight, steel ball contact with the circular raceway at four point, it can bear the axial force, radial force and the tilting moment at the same time .
It can be used for slewing conveyer, welding manipulator, light & medium duty crane, excavator, and other construction machinery .
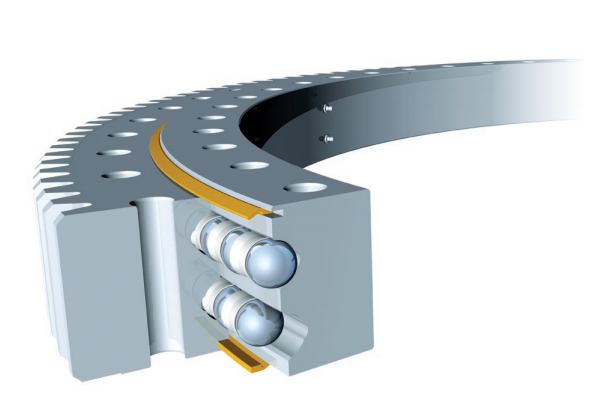
2) Double Row Ball Slewing Bearing
Characteristic of structure, performance and application
Double row ball slewing bearing has three seat ring, the steel ball and the spacing block can be directly arrange into the upper and lower races, two rows of upper and lower steel balls with different diameter are fitted according to the stress condition .
This kind of open assembly is very convenient, for the upper and lower bear raceway arc angles is 90°,which can bear large axial forces and tilting moment . When the radial force is greater than 0.1 times the axial force need to be specially designed the raceway .
Double row different ball slewing bearing’s axial and radial size are relatively large and solid in structure, so it is specially suitable for the medium diameter tower cranes, truck mounted cranes etc . loading and unloading machinery .
3) Three Row Roller Slewing Bearing
Characteristic of structure, performance and application
The three row roller slewing bearing has three seat rings, which separate the
upper, lower and radial
raceways, it made each row of the roller’s load capacity can be specified and can bear different loads simultaneously . The capacity load is the largest one compare with the other three models . Due to the large size in axial and radial dimension & the solid structure, it is specially suitable for the heavy duty machinery such as wheeled excavator, wheeled crane, ship crane, ladle turrets and the heavy duty mobile crane etc .
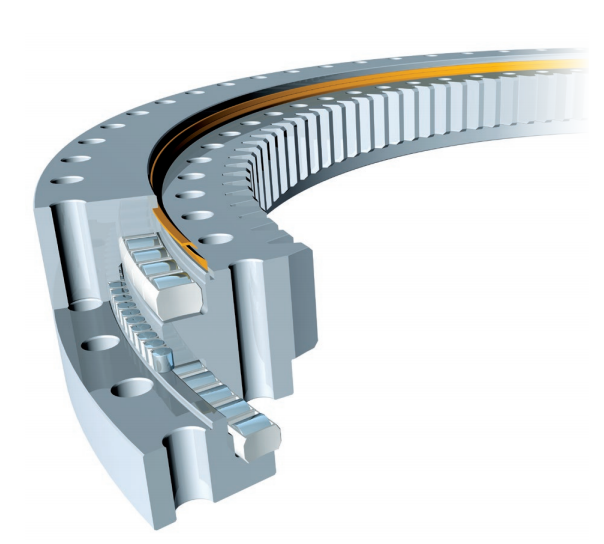
4)Cross -roller slewing bearing
Characteristic of structure, performance and application
Cross -roller slewing bearing consists of two seats. The structure is compact, light weight, high manufacturing accuracy, small in assembly gap, and high requirements for installation accuracy. Larger radial force. It is widely used in large rotary devices such as bartebling machines, overweight transportation machinery, port machinery, mining machinery, construction engineering machinery, park entertainment machines, installation machines and missile launchers.
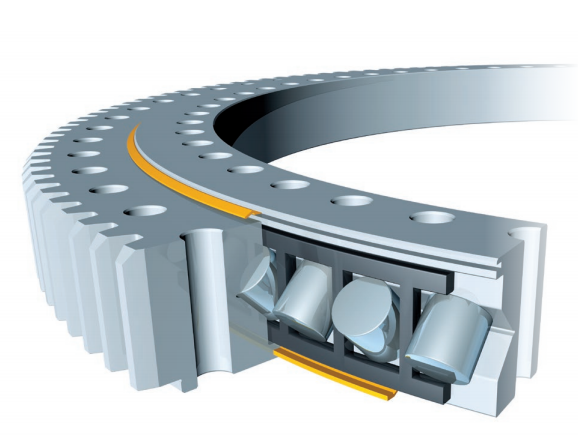
2.Technical requirements
(一) material and technical parameters of slewing bearing
1, material
1) the ring adopts 42CrMo-GB/T 3077, but also can adopt other materials with good normalizing, quenching and tempering and induction hardening performance
2) the rolling body adopts GCCR15, conforms to the GB/T 18254-2002 regulation.
2.Hardness
1) the hardness of the matrix, the hardness of the quenched and tempered ferrule is 229HB ~ 269HB.
2) raceway surface hardness and layer depth, raceway surface hardness after medium frequency induction hardening is 55HRC-62hrc, bearing raceway effective hardened layer depth DS ≥3.5 mm (raceway surface hardness ≥48HRC)
3) surface hardness of gear, the hardness of induction hardening of tooth surface and tooth root is 50HRC-60hrc, the effective hardening depth DS of tooth surface is 1.5-3.0 mm, the effective hardening depth DS of tooth root is 1.0-3.0 mm, the effective hardening depth DS (hardness ≥40HRC)
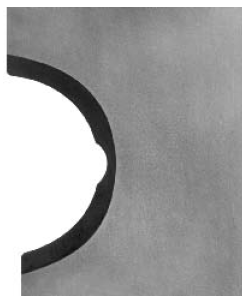
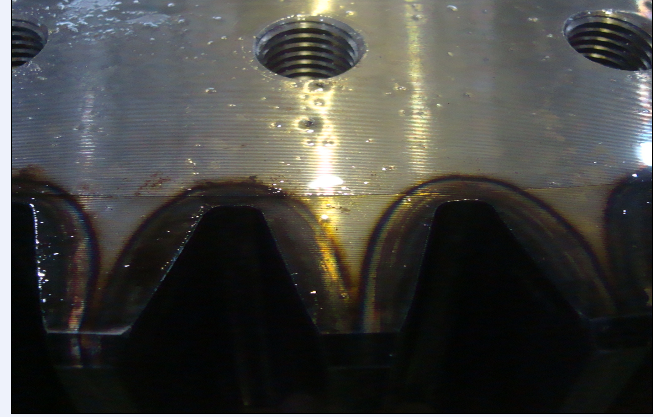
(二)Design, calculation and check of the roller, raceway, Bolt and gear of the slewing bearing
1, steel ball diameter,
In the raceway cross-section size allowed, the appropriate increase of steel ball diameter, to a certain extent, can improve the bearing capacity of the slewing support.
The Raceway
Calculating the rated static load and rated dynamic load of the slewing bearing according to ISO76:2006 and ISO281:2007; calculating the equivalent FA and equivalent M of the slewing bearing under static and dynamic conditions, respectively, the static load curve and dynamic load curve of the slewing bearing are used to select the static Factor of safety and fatigue life of the bearing respectively, both the minimum static Factor of safety and the minimum dynamic Factor of safety are required to be greater than or equal to one at their maximum limit loads
3, bolts
Firstly, the calculated load of bolts is converted into equivalent load, then the ultimate load curve of the bolt (which is determined when the clamping length of the bolt is 5 times the nominal diameter of the bolt and the pre-tightening force is 70% of the yield limit of the bolt material) is used to check the bolt under the condition of maximum ultimate load Then according to VDI2230 under the static or alternating load of the bolt connection to check, to prevent the failure of the connection may cause serious losses.
(三)Four main parameters which affect the bearing capacity of slewing bearing
There are two failure forms of slewing bearing, one is raceway damage, the other is broken teeth. The damage of raceway accounts for more than 98% , so the quality of raceway is the key factor that affects the life of slewing bearing. Raceway hardness, hardened layer depth, raceway curvature radius and contact angle are the four most important factors affecting raceway quality.
Rolling road hardness
Raceway hardness, raceway quenching hardness of rotary bearing has great influence on its rated static load. If the rated static load is 1 at 55HRC, the corresponding relationship between the rated static load of bearing and raceway hardness is as follows.
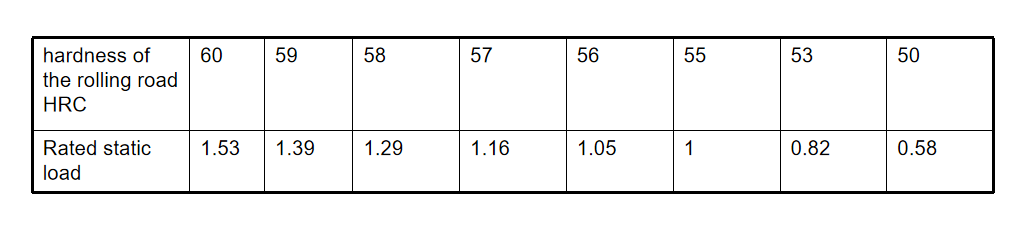
2.The hardened layer depth of raceway
The necessary depth of hardened layer is the guarantee that no spalling occurs in the raceway of rotary bearing. When the slewing bearing bears the external load, the steel ball and the raceway change from the point contact to the surface contact, the contact surface is an elliptical surface. In addition to the compressive stress, the raceway is also subjected to shear stress, and the maximum shear stress occurs at a depth of 0.47 a below the surface (the semi-major axis of the contact ellipse) , this is why the standard defines the depth of the hardened layer according to the diameter of the ball rather than the diameter of the slewing bearing. The minimum guaranteed value is given in the standard. The static load C of the bearing is proportional to the depth of hardened layer H0.908. If the depth of hardened layer required to be 4mm is only quenched to 2.5 mm, then the static load C of the bearing will be reduced from 1 to 0.65, the probability of failure of slewing bearing due to fatigue spalling will be greatly increased
3.Radius of curvature of raceway
The radius of curvature of raceway is the radius of curvature of raceway in vertical section, the ratio of“t” to the radius of the steel ball also significantly affects the rated static load and fatigue life of the slewing bearing. If t = 1.04, the rated static load and fatigue life are both 1, then the relationship between the rated static load and fatigue life of the slewing bearing and T is as follows.

As can be seen from the above table, the greater the radius ratio, the lower the rated static load, the shorter the service life.
4, raceway contact angle
contact angle refers to the ball in the raceway on the contact point and the ball center of the line with the rotating support radial section (horizontal plane) between the angle. The rated static load C of the slewing bearing is linearly proportional to SIN α, and the original contact angle is usually 45 ° . When the slewing bearing has gap, the actual contact angle is larger than the original contact angle, the larger the gap, the greater the actual contact angle. In the range of clearance specified in the standard, the contact angle will increase by 2 ° ~ 10 ° , that is, the actual contact angle will reach 47 ° ~ 55 ° , which is a favorable change to the bearing capacity. However, if the original contact angle and the gap are large, the actual contact angle will exceed 60 ° , and the gap will further increase with the wear of the raceway, and the actual contact angle will also increase, the actual stress of the raceway will be higher than the theoretical stress, which will cause the raceway edge collapse and the slewing bearing failure.
(四)(4) for the application environment with large sloshing, the improvement measures of slewing bearing are needed
1) proper reduction of bearing clearance, especially axial clearance.
2) control the shape of bearing raceway, especially the ellipticity.
3) strictly control the surface hardness and hardened layer depth of bearing raceway to prevent the appearance of too low surface hardness, layer depth, too shallow.
4) improve the hardness of the base material of the bearing.
5) other factors. After using for a period of time, due to the plastic deformation of the bearing raceway and the increase of the clearance, it is normal for the equipment to swing relatively large.
3.Installation and maintenance
1.Avoid any solvents from being exposed to a sealing ring or entering the roller. Do not paint on the seal belt. The surface contact surface connected to the support must be cleaned up.
2.There are no welding tumors, burrs, paint and other adhesives. There should be no lubricating oil on the surface and must be kept dry.
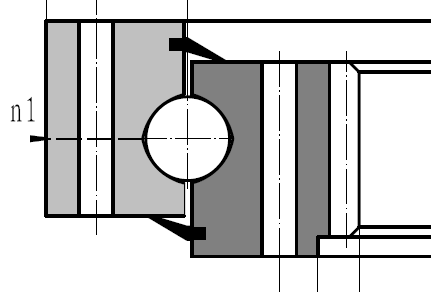
3.During installation, the quenching soft band should be outside the main load area.
4.Pre -bolts should be installed in a star -shaped shape. Symmetrically continuously in the 180 ° direction, and finally pass it through to ensure that the bolts on the circular cycle have the same pre -tightening force.
It is strictly forbidden to use the spring cushion ring.
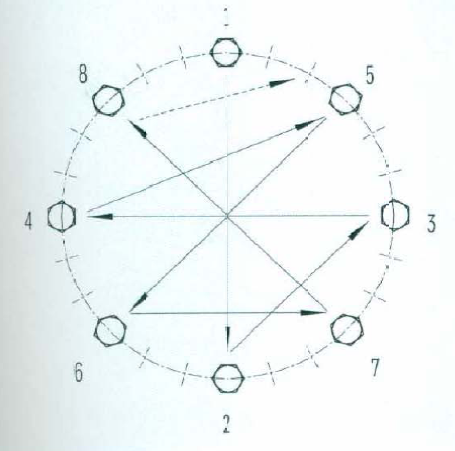
5.Gear mesh clearance
For the rotation support of the tooth, the tooth side gap is adjusted according to the highest point of the radial jump of the gear festival (three teeth with red paint). The minimum value of the side gap is generally 0.03 ~ 0.04 × modulus. After the final tight support, the gear meshing of the small gear on the entire circle must be re -inspected.
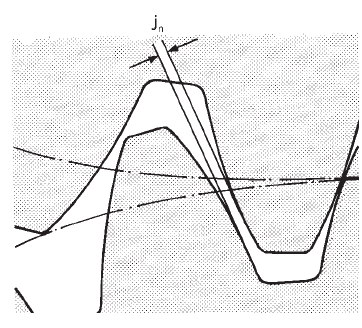
6.Lubrication
1) on delivery, the raceway is coated with a small amount of No. 2 lithium grease. The user should refill the raceway with new grease according to different working conditions.
2)The first lubrication of the teeth must be performed immediately after installation. Tooth surface must have sufficient lubricant film.
3) the raceway should be filled with grease regularly. General ball slewing bearing every 100 hours of operation should be added grease, roller slewing bearing every 50 hours of operation should be added grease. In the high temperature or more dust and other special working environment of the support, should be appropriately shortened replenishment period. Equipment before and after a long time to stop running, it must also add sufficient grease. The Raceway must be filled with grease each time until it oozes from the seal.
7, check the bolts, installed and put to work in 100 hours of continuous operation, should fully check the installation of bolts pre-tightening force is in line with the requirements, after every 500 hours of continuous operation repeat the above-mentioned inspection.
8、Check the seal system. The tape and seal system must be checked at least once every 12 months. In proper operation, the tape must remain undamaged. When cleaning components, the detergent should be avoided contact with the sealing tape or into the raceway system.
4.Rotation accuracy of slewing bearings
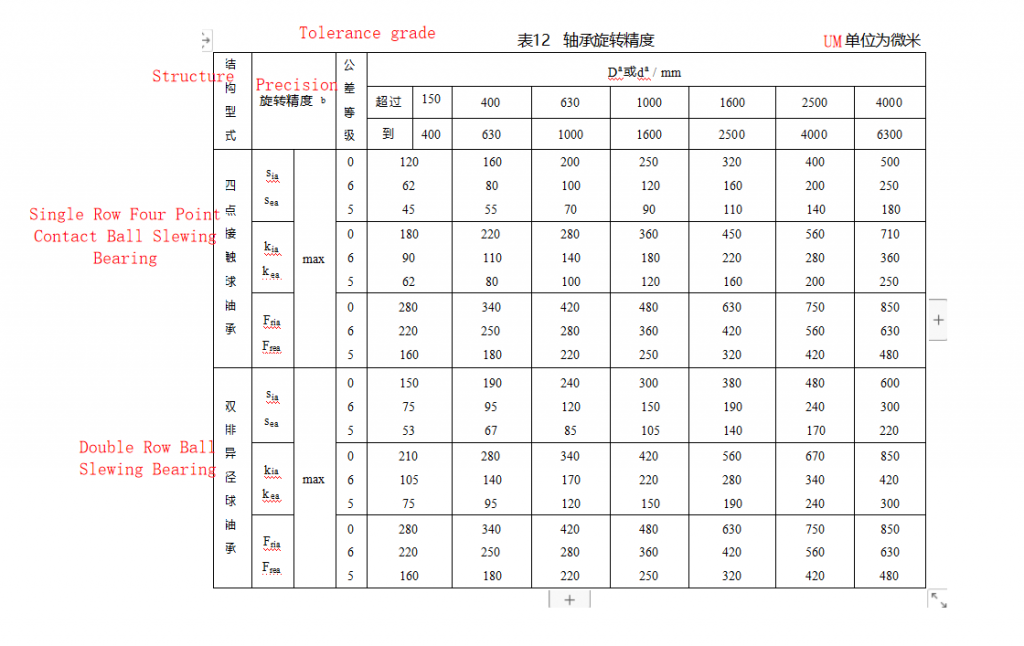
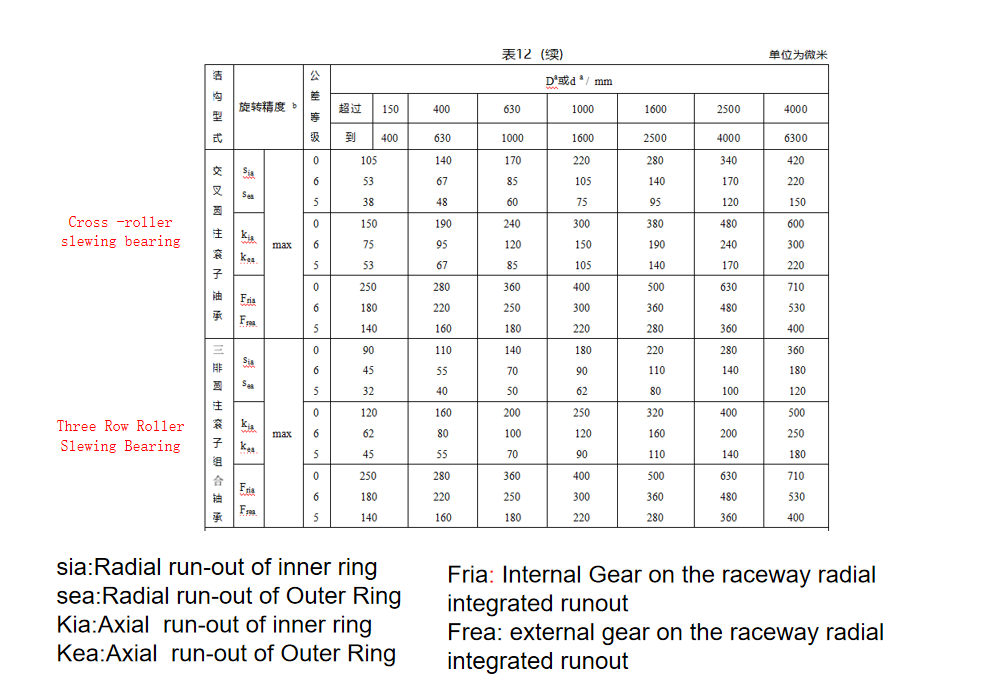
5.Axial clearance of slewing bearings
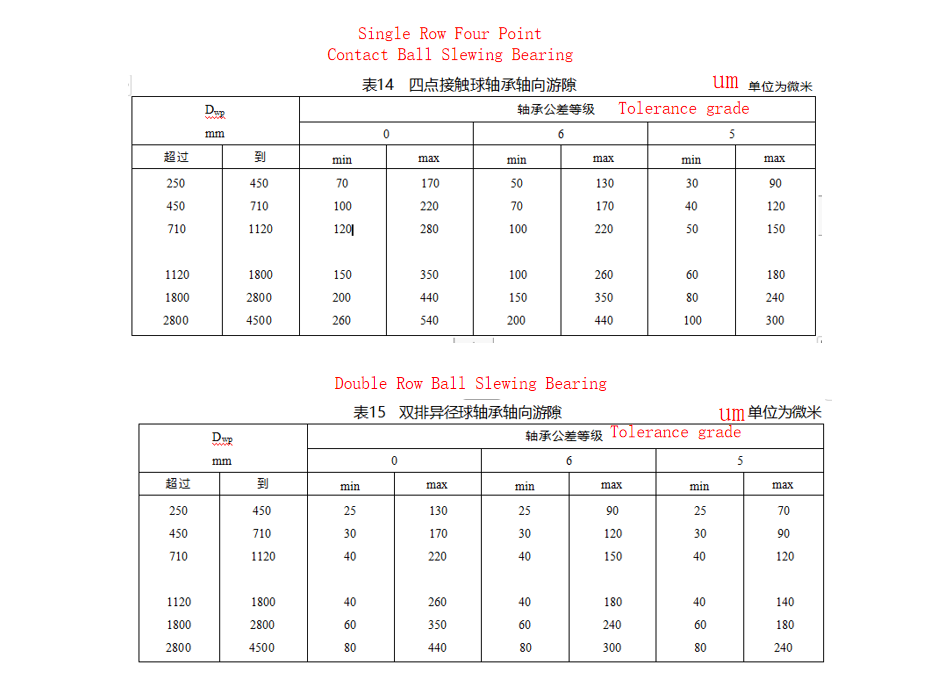
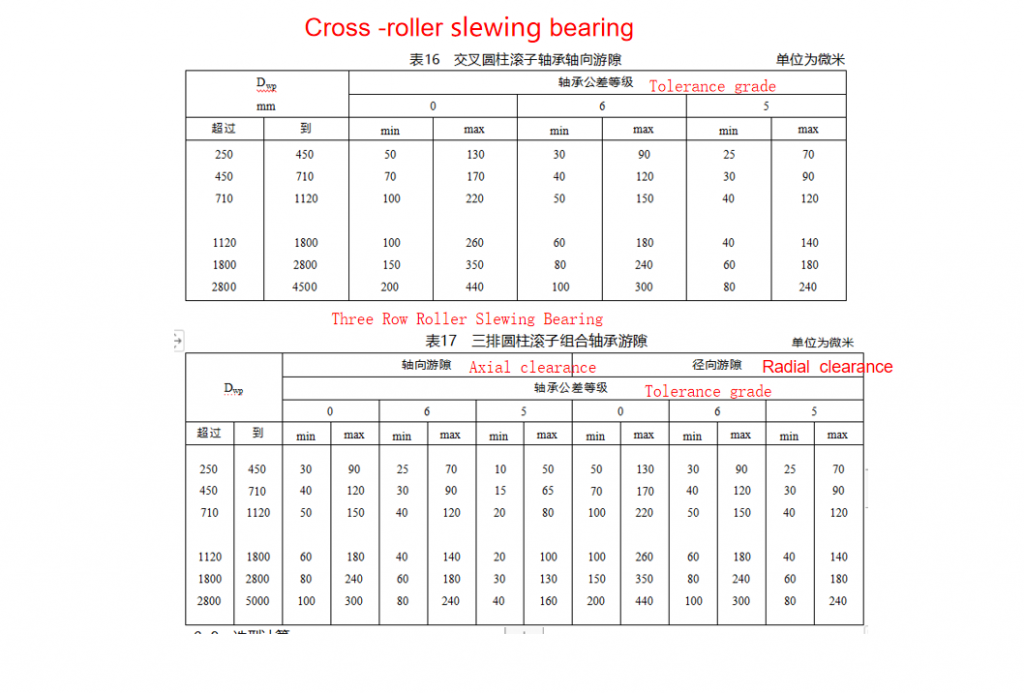