3、Corrosion resistance of bearings
Bearing rust is a common problem for us. There are many factors that cause bearing rust, such as ambient temperature, temperature, the PH value of coastal air, the performance of anti-rust oil, and packaging protection. Regarding bearing steel, the corrosion resistance of bearing steel from high-quality steel plants is relatively better. Bearing processing and surface roughness also affect the corrosion resistance of the bearing. The smoother the surface, the stronger the corrosion resistance. Industries that have special requirements for corrosion resistance include food, chemical, and medical. The usual solution to improve corrosion resistance is to use stainless steel or non-metallic materials.
1. Martensitic stainless steel
The commonly used SUS440\SUS420 (corresponding to the domestic code is 9Cr18\3Cr13) is martensitic stainless steel. Martensitic stainless steel can obtain high hardness through heat treatment, 420 reaches about HRC55, and SUS440 reaches HRC58 and above. Martensitic stainless steel is actually rusty, commonly known as “stainless iron”. The corrosion resistance of stainless steel is evaluated by salt spray test. The SUS440\SUS420 salt spray test will rust in less than 20 hours.
SUS440 and SUS420, improve its corrosion resistance, the solution is passivation treatment. After the passivation treatment, the salt spray test can reach 150 hours without rust, and it can reach 200 hours without rust when done well.
“Bearing steel” is the name of a material family. There are many specifications and models. Steels with a carbon C content of 1% and a chromium Cr content of 1.5% or more can be called bearing steels. We usually consider bearing steels to be GCr15 by default. .The two kinds of stainless steel mentioned above, SUS440 and SUS420, of which SUS440 is a kind of bearing steel, the performance of the product made by it will not be reduced compared with bearing steel. But SUS420 is different, because it has low carbon content and the heat treatment hardness is not up to the standard of bearing steel, and the bearing performance will be lower than that of bearing steel.
The domestic market for small and medium stainless steel bearings is mostly SUS420, and it also means to pretend to be SUS440 (because the price of 440 is about 8,000 per ton), the hardness is made high, and the hardness is close to HRC58. The hidden danger that has never been brought is that the ferrule is too brittle Fragile, cracking of the outer ring often occurs when the dust cover is pressed during the manufacturing process.
2. Austenitic stainless steel
Austenitic stainless steel is represented by SUS316 and SUS304, which cannot be obtained by thermal treatment. It is very soft compared to bearing steel, but has super corrosion resistance and will not rust. The public toilet is used Austenitic stainless steel.
Its hardness is not enough, the bearing load capacity is very low, and the speed is also low. The size is not very accurate, and the turning feel is not smooth. Kaka will not rotate flexibly when falling from the table. Bearings made of SUS316 and SUS304 can only be used under conditions where load and speed are not required. The price is many times more expensive than ordinary bearings. There is a small amount of demand in the market for stainless steel bearings like this, and there are also manufacturers who produce them. The price is not cheap. Where can I go about it?
3. Non-metallic materials
The non-metallic materials used for bearings are plastics and ceramics. Plastics and ceramics do not have corrosion problems, but the rotation accuracy, noise, load, and speed performance are much worse than ordinary bearings. It can only be used under conditions that require very low load and speed. The price is many times more expensive than ordinary bearings.
4、High temperature resistance of bearings
The maximum temperature of ordinary bearings does not exceed 140°C. I did a test before and found that when the bearing temperature reaches 140°C, the bearing will burn and turn yellow, and it will fail after less than 10 hours. The long-term operating temperature of the bearing does not exceed 120°C. Like the SKF official website and samples, it states that the working temperature is -20℃~110℃.
The working environment temperature of the bearing, plus the temperature rise of the bearing itself. Bearings whose operating temperature can reach 120°C are not available for ordinary quality products. The temperature rise of the bearing is explained here: when the bearing is running, the temperature of the bearing itself will be higher than the ambient temperature, and the higher the temperature, the worse the quality of the bearing. That is to say, customers often say that your bearings are easy to get hot (that is, the temperature rises). Temperature rise is also an indicator for evaluating bearings. This item is not very popular, and ordinary manufacturers do not have this detection capability. There are standards for temperature rise.
The working environment temperature of the bearing may be higher than the actual data given by the customer. This is also my previous thought. For example, the bearing installation position will be a certain distance from the heat source, and the temperature will be much lower than the heat source, but the customer will regard the heat source temperature as the working temperature of the bearing. For example, for bearings used by customers, the grease added is very poor, and the dropping point is very low. The grease will drip into liquid when the temperature is not high, and the bearing will fail. In this case, high temperature bearings are required. We can replace them. Regular brand high-temperature grease to test. The following summarizes some common methods for high temperature bearings.
1. High temperature tempering
The heat treatment and tempering temperature of bearing steel is 180°C (required in the textbook), but some manufacturers only have 160°C in actual operation. The operating temperature of the bearing is the tempering temperature minus 50°C. High temperature tempering means that the tempering temperature is higher than 180°C. Bearings with high temperature tempering are suffixed with the model name: S1, S2, S3, S4
2. Use ceramic bearings
The working temperature of ceramic material silicon nitride (Si3N4) can reach 1100℃
The working temperature of zirconia (ZrO2) can reach 600℃
The working temperature of ceramic bearings is restricted by the material of the cage. For example, the working temperature of the cage made of PTFE or PEEK is only 260°C. If the working temperature exceeds 260℃, the cage can only be abandoned and a full-ball cageless structure is adopted.
The performance of ceramic bearings is not comparable to other performances of bearing steel materials except for high temperature. Ceramic bearings can only be used under working conditions where low speed, low load and rotation accuracy are not essential.
3. The temperature resistance of the sealing ring and plastic cage of the bearing (commonly used)
3.1 The default material of the sealing ring is nitrile rubber NBR, the maximum working temperature is 120℃,
3.2 The highest working temperature of polyacrylic resin ACM is 160℃, which is widely used in automobile bearings, such as automobile tensioner bearings, automobile generator bearings, and automobile clutch bearings.
3.3 The maximum working temperature of fluorine rubber FKM for automobile bearing seals and microwave ovens is 260℃,
3.4 Nylon cage PA66, the highest working temperature is 120℃,
The maximum working temperature of PA46 is 160℃.
The working temperature of the cage made of PTFE or PEEK is 260℃.
Full ball with loading gap without cage
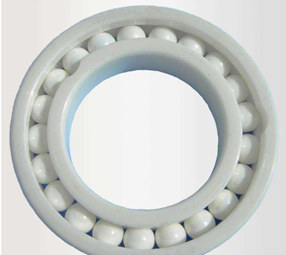
5、Sealing performance of the bearing
The sealing performance depends on the design and processing quality of the sealing ring and the dust-proof groove. The factors that affect the sealing performance are:
1. Is the sealing ring made according to the drawing? This is very important. At present, domestic manufacturers have the ability to design seal rings, and there are very few seal rings produced according to the design. Most manufacturers, the bearing factory send the prepared open bearing samples to the seal ring manufacturer to open the mold to produce the seal ring. As long as the bearing can be covered, it is not tight or loose, and the bearing does not rotate too tightly. , I don’t care if it leaks fat.
2. The rubber material has a considerable influence on the sealing performance. The rubber is too hard to wear and temperature, and it will age when it exceeds 80°C. The same is nitrile rubber. There are 12/kg and 25 yuan/kg on the market.
3. The grease itself is easy to leak. Grease with a low dropping point tends to leak.
4. The bearing product’s own structure problem. Larger rolling elements are more prone to leakage than small ones, plastic cages are more prone to leakage than steel cages, and those whose cage is closer to the sealing ring are more prone to leakage.
5. The processing quality of the dust-proof groove. Dimension, roughness, shape and position tolerance.
6. The problem of bearing working conditions. The rotation speed is higher than the lower, and the outer ring is more likely to leak than the inner ring. The higher ambient temperature is more likely to leak.
When encountering customers who have requirements for sealing performance, it is inevitable to choose the right supplier. 1. Sealing ring design and processing capabilities; 2. With dust-proof groove structure in the inner ring, size, roughness, shape tolerance, etc. must be Meet the design requirements; 3. Choose grease with a high dropping point; 4. Add as little as possible within the specified range of the amount of grease.